Welcome to the Sonal Track Factory
Here at SonalTrack, as an expert GPS tracker manufacturer in China, the automated factory is at the heart of our business. We pride ourselves on providing even more valuable support to our partners worldwide through the optimization and refinement of all aspects of our business.
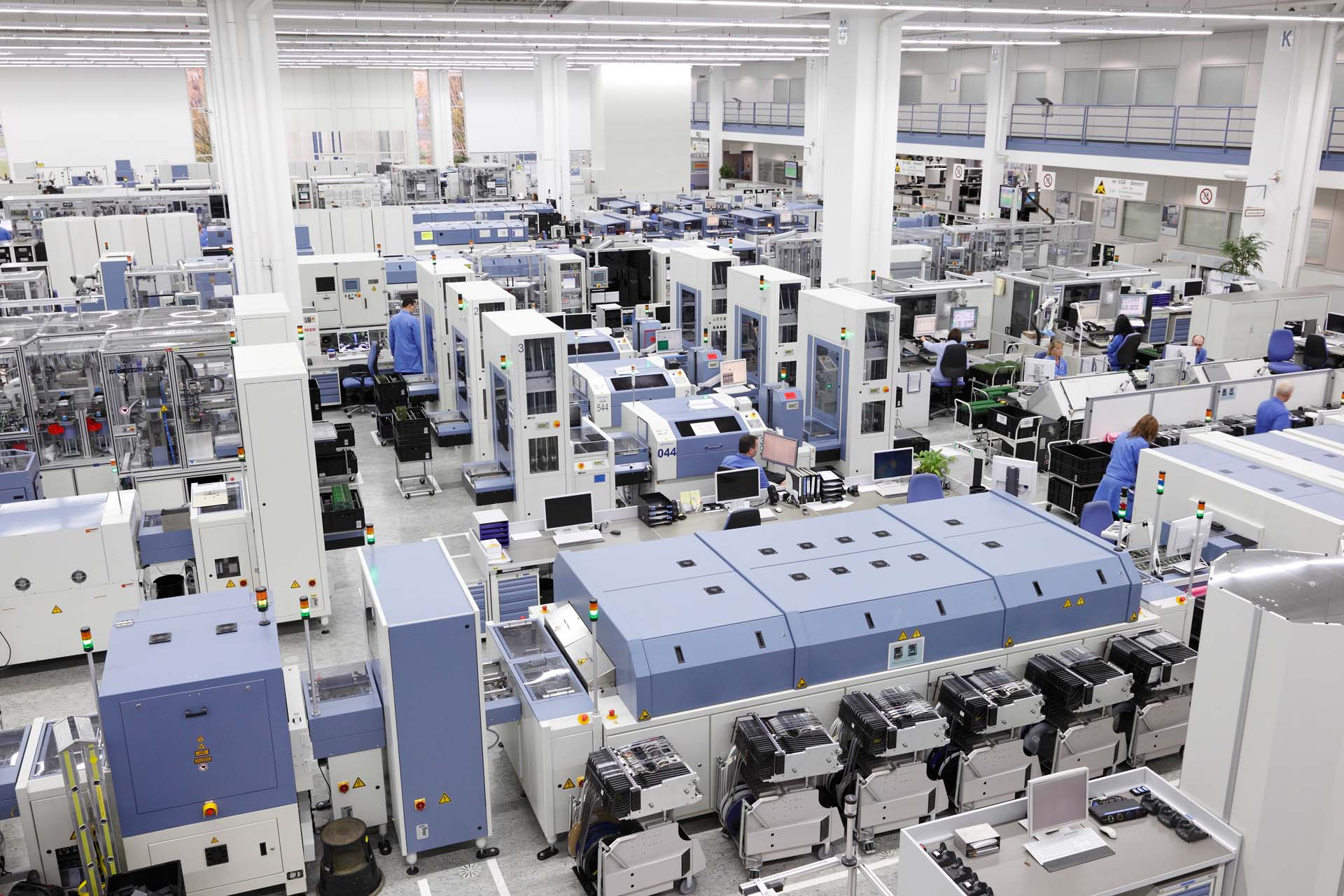
-
2 Manufacturing Plants
-
1.5KM”2 Factory Space
-
300+ Factory Staff
-
8 High Speed SMT Line
-
5 Assembly Lines
-
10+ Experience
Sonal Track Manufacturing
With10+ years of development since our establishment in September 2009, SonalTrack has achieved a unique status amongst leading suppliers of vehicle GPS tracking products in the global vehicle tracking system market segment. Our humble beginnings as a single-man operation had limited potential and promise; however, it soon became apparent that the company was on to something big. Our ingenious technology made vehicle tracking devices easier to use and more effective for enterprise use than ever before. With virtually no marketing budget, we developed a truly remarkable global reputation in our field.
Original Equipment Manufacturing (OEM)
From Main Electronic Service to end products all directly to you
● Complete industrialization of new products
● Supply chain and logistics
● SMT assembly –two full automatic SMT assembly lines
● Automated optical inspection (AOI) and visual inspections are made for each device
● Wave soldering – RoHS and Leaded
● Selective soldering – Lead free
● PCB marking with laser – 100% trackable
● Stencil production
● X-Ray Inspection – BGA and PCSs are checked using X-Ray test
● Conformal coating and PCB washing
Quality Management
12 times quality inspections, 36-hour aging testing, tracker qualified rate at a high level of 99.5%, and maximum trouble-free operation time of 43,800 hours.
IQC
● Inspect all accessories and main materials to ensure zero defects.
● Adopt United States defense standard MIL-STD-105E(2)
SMT QC
● Reflow soldering with 8 high temperature zones
● Multi-functional SMT machine(JUKI); Support minimum size:0201
● AOI inspection after reflow soldering
Aging Inspection
● All products are passed 36 hours
● High temperature aging treatment room
DIP QC
● Inspect pseudo soldering and non-soldering
● First article inspection
GPS Tracker QC
● QC of semi-finished products
● Test the working mode of semi-finished products, such as the call-and vibration functions
● Simulate the base station to send GSM Signals to ensure positioning accuracy and data consistency
Packing QC
● IPQC inspectors monitor the whole production process
● OQC inspectors randomly inspect products
● Rework unqualified products
Finished Goods Inspection
● Test product performance
● Inspect product appearance
● Make records
OQC
● Label raw materials
● Use the high-end electrical testing record system to inspect the products
● Adopt comprehensive ERP system to ensure high-efficiency management